“Grooving Machines: Technological Revolution Boosting Efficiency and Sustainability in Industrial Production”
Grooving machines, specialized tools designed for cutting grooves into various materials, possess technical features that significantly impact production processes in multiple industries. Understanding these technical specifications and their effects on manufacturing can highlight the versatility and efficiency these machines bring to the table.
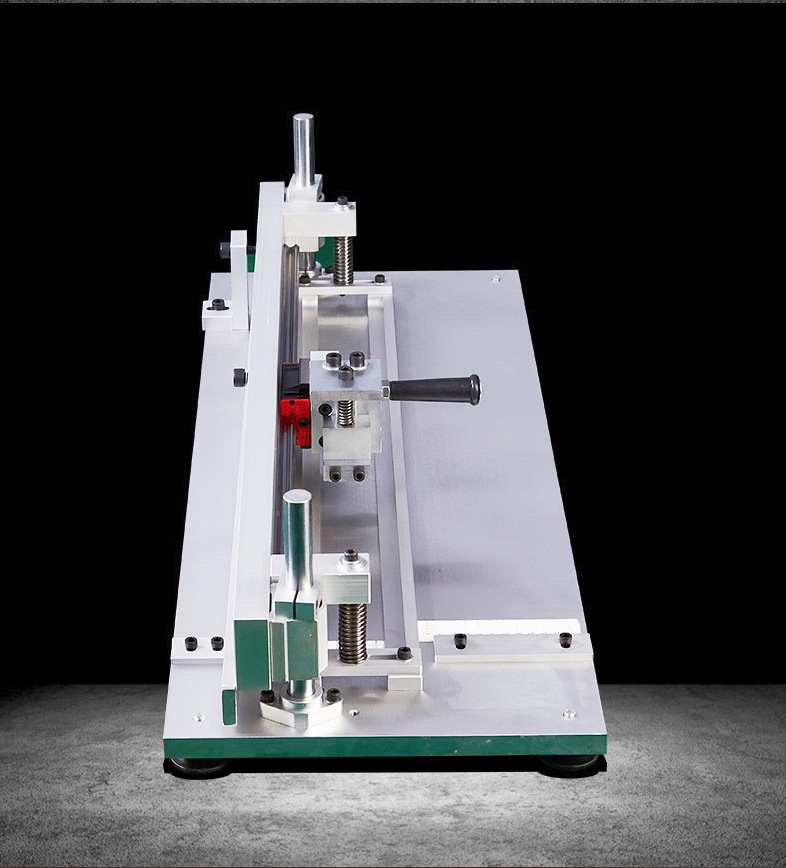

Technical Specifications of Grooving Machines:
- Precision and Accuracy: Grooving machines, especially those integrated with CNC technology, offer high precision and accuracy in cutting grooves. This ensures that components fit together perfectly, reducing waste and improving product quality.
- Speed and Efficiency: The ability to quickly produce grooves without sacrificing quality means that production timelines can be significantly reduced. This increases overall manufacturing efficiency and allows for higher output rates.
- Material Versatility: Modern grooving machines can handle a wide range of materials, from metals and plastics to composites and wood. This flexibility allows manufacturers to use them across various applications, making the machines highly versatile.
- Depth and Width Control: The capability to adjust the depth and width of grooves with high precision allows for customization and adaptability in production, meeting specific design requirements for different projects.
- Automated Operations: With advancements in technology, many grooving machines now come with automated features, reducing the need for manual adjustments and minimizing human error. This automation also contributes to labor cost savings.
- Energy Efficiency: Newer models are designed with energy efficiency in mind, helping reduce operational costs and contributing to more sustainable production practices.
Impacts on Production:
- Enhanced Product Quality: The precision and accuracy provided by grooving machines ensure high-quality finishes and fittings, leading to superior end products.
- Increased Production Capacity: Faster production times enabled by the speed and efficiency of grooving machines allow for larger volumes of products to be manufactured within shorter periods.
- Cost Reduction: The reduction in material waste, coupled with energy-efficient operations and automated features, leads to significant cost savings in the long run.
- Flexibility and Customization: The ability to easily adjust groove dimensions and work with various materials allows for greater flexibility in production, enabling the manufacturing of customized products.
- Sustainability: By minimizing waste and optimizing energy use, grooving machines support more sustainable manufacturing processes, aligning with environmental goals and regulations.
In summary, the technical features of grooving machines have a profound impact on production by improving efficiency, reducing costs, and enhancing product quality. As these machines continue to evolve with technological advancements, their contribution to the industry is expected to grow even further, making them indispensable tools in modern manufacturing.